d Packing and Shipping Procedures
Establishing Shipping Guidelines
Establishing Shipping Guidelines
Establishing shipping guidelines for packing and shipping procedures is essential to ensure that goods are delivered safely and on time. It's critical to consider factors such as cost, size, weight, fragility & security when setting these polices. Cost is often a major consideration; freight charges can be expensive and need to be calculated in order to remain competitive (yet profitable). Size and weight of the shipment must also be taken into account; larger items require bigger boxes or crates while heavier products might necessitate specialised handling equipment. Fragileness of certain items should not be overlooked either - they may need extra padding or cushioning for protection during transit. Security is another important element that needs attention; goods should be secured tightly with straps, shrink wrap etc., so they don't move around unnecessarily inside the container.
Furthermore, having clear instructions regarding delivery addresses & contact details is crucial. Also, it's advisable to have written proofs of delivery in case any dispute arises between customer & seller! Additionally, providing tracking numbers allows customers to track their orders in real-time and reduces chances of lost shipments significantly. Finally, regularly reviewing shipping policies helps maintain high standards of efficiency and customer satisfaction over time - this might demand periodic updates depending on changing market trends or new business requirements. To conclude, establishing effective shipping guidelines is fundamental for successful packing & shipping operations!
Pre-packing Procedures
Pre-packing Procedures are essential for any product shipment. It is (important) to ensure the package's safety and security during transit. First, all items must be inspected, including measuring their size and weight! If there is an irregularly shaped item, it must be securely wrapped so that it doesn't move around or break inside the shipping box. Additionally, fragile items should always be marked as such and packed with extra padding material to reduce the risk of damage in transit.
Futhermore, any liquids must be properly enclosed in a sealed plastic bag and placed into a sturdy container before packing them into the main box. This will help prevent leakage from causing any potential issues during shipping. Finally , labels should always be affixed onto each box clearly stating what is inside as well as providing instructions on how to handle it correctly. Moreover, if hazardous materials are included in the shipment they have to be labeled accordingly in order not to put anyone at risk !
In conclusion, pre-packing procedures are necessary for all shipments and can help prevent many problems from arising during transit . By following these steps carefully every time you ship something out you can protect your products from getting damaged while also helping keep everyone safe!
Packaging Materials Selection
Packaging materials selection is an important part of the packing and shipping procedures. It is essential to choose the right material in order for a shipment to reach its destination safely and securely. There are several considerations that must be taken into account when selecting packaging materials, such as cost, durability, weight and size.
It's also necessary to consider what kind of protection the product needs from heat, cold or moisture. Different products require different types of packaging materials; for example, fragile items usually require extra padding or cushioning to prevent them from being damaged during transit. Moreover, certain items may need specific labels like 'Fragile' or 'Handle with Care'.
Furthermore, it's important to ensure that all packing materials used meet safety standards and regulations (for instance, paper-based materials should be made from recycled content). On top of this, if any hazardous substances are contained within the package then special precautions must be taken to ensure they don't leak out or cause harm while in transit. Additionally, it's worth considering using biodegradable packaging materials wherever possible - not only is this better for the environment but can also help cut costs!
All-in-all, choosing the appropriate packaging material requires careful thought and consideration(s). There are many factors which must be taken into account so that shipments arrive at their destination safe n' sound!
Labeling and Documentation Requirements
Labeling and documentation requirements for packing and shipping procedures are an essential part of the process! The correct labeling and documentation is critical to ensure that shipments arrive in a timely manner, with no complications. Part of the procedure involves properly preparing all items for transport (e.g., using protective packaging material). It's also important to accurately label each package, so that it can be tracked throughout its journey. Additionally, accompanying paperwork must be filled out correctly and accompany the shipment, providing details about what is being shipped as well as who is receiving it.
Furthermore, failure to adhere to labeling and documentation guidelines may result in delays or even sanctions from regulatory bodies. Hence, workers involved in packing and shipping need to understand their obligations according to applicable laws and regulations. They must use appropriate forms for delivery documents such as bills of lading, invoices etc., ensuring that they contain accurate information; otherwise they could incur hefty fines or other penalties!
Therefore, organizations should implement policies regarding packing and shipping procedures that include specific instructions on labeling and documentation requirements. These should cover issues ranging from how to package goods safely, through adhering to labeling standards - including barcodes - right down to which forms must be used when sending shipments overseas. By doing this they will protect themselves against potential problems caused by improper packing or incorrect paperwork!
In conclusion, proper labeling and documentation is key when it comes to successful packing and shipping procedures; organizations should take every step necessary to ensure these are met at all times.
Choosing a Shipping Carrier
Choosing a shipping carrier is an important part of packing and shipping procedures. There are many factors to consider when selecting the right one for your needs. You may want to look at delivery times, cost savings, customer service (if available) and insurance options. It's essential to make sure that the carrier you choose can meet all of your requirements!
One way to narrow down the choices is to research online reviews or talk (to) people who have used different carriers. This will give you some insight into their experience with the company and help you decide which one is best suited for your needs. Additionally, it may be worth considering whether the carrier offers tracking services or other features that could benefit you in terms of safety and convenience.
Furthermore, another factor to take into account when selecting a shipping carrier is reliability. In this regard, it might be worth looking into how long they have been in business and what kind of reputation they have amongst others in the industry. Additionally, if there are any special discounts offered by certain carriers then this could also be beneficial in terms of saving costs on your shipment. Moreover, don't forget about any extra fees such as fuel surcharges or additional charges for oversized packages!
In conclusion, choosing a shipping carrier requires careful consideration of various factors such as delivery times, cost savings, customer service and insurance options among others. Researching reviews online or talking with people who have used various carriers can provide valuable insight into their experiences with each company and ultimately help you select the most appropriate one for your needs! With this knowledge in hand, you should be able to confidently choose a reliable shipping carrier that meets all your requirements without breaking the bank!
Tracking Shipments and Delivery Processes
Packing and shipping procedures can be tricky, but with the right strategy they don't have to be! Tracking shipments and delivery process is key (but often overlooked) for businesses that ship products or materials. By tracking these processes, you can ensure that your packages reach their destination quickly and securely.
To start, it's important to create a packing list for each parcel you send out. This will help you keep track of exactly what items were sent in each package. You'll also want to label everything clearly with the recipient's address as well as any special instructions. Once your items are packed and labeled, it's time to get them shipped!
You may choose to utilize different shipping services depending on your needs. Some services offer expedited shipping or insurance while others prioritize affordability. Whichever option you select, tracking capabilities should be included in order to monitor the whereabouts of your parcels throughout transit. Many companies offer real-time order tracking so that you know exactly when items are delivered - this feature can give great peace of mind!
In addition, many shippers now provide digital proof of delivery which includes a signature from the receiver confirming receipt of an item. This extra layer of security is very helpful when sending valuable items such as electronics or jewelry - ensuring that nothing goes missing en route! Plus, by having records of all shipments and deliveries, it helps make future orders easier too since there's no need to reenter information every single time something gets shipped out.
Overall, tracking shipments and delivery processes is a vital part (but often neglected) part of the packing & shipping procedure process. It not only provides assurance for both sender and receiver but also makes reordering simpler & more efficient going forward!
Post-shipment Procedures
Post-shipment Procedures(for Packaging and Shipping) are essential to ensure that goods have been safely delivered. They involve examining the condition of the items when they arrive, and making sure they have been handled correctly. Negligence can lead to costly damages which could've been avoided! It's important to check for any signs of wear or tear, as well as any missing pieces. (Also be aware of any customs fees that may apply).
If all is in order, then a quick inspection should suffice. A more thorough examination might be necessary if there appears to be an issue with the shipment. This includes looking over all paperwork and invoices to make sure everything was ordered accurately and received properly. Documentation such as proof of delivery should also be double-checked for accuracy.
In addition, it's important to follow up on customer inquiries in a timely manner - this will help build trust with them and maintain good relationships! If there were any problems during transit, then corrective actions need to be taken immediately. Also, it's wise to keep track of every shipment via tracking numbers so you'll know where your packages are at all times.
Overall, post-shipment procedures(for packing & shipping) are vital for ensuring that products arrive safely and on time! Properly handling them is key for maintaining smooth operations within a business - so don't forget about them!
Maintaining Records of Shipments
Maintaining records of shipments is a critical part of any packing and shipping procedure. It ensures that packages are delivered to the right customers, on time, and in good condition. (Negation) Without appropriate tracking information, it's impossible to know where a package is or when it will arrive! Keeping meticulous records helps streamline processes and reduces delays.
Using systems like bar codes or RFID tags makes for efficient data collection. Scanning these items creates detailed logs with exact arrival times and locations. This data can be used to quickly identify problems should they arise. Additionally, thorough record-keeping provides valuable insights into customer service performance, allowing companies to make improvements accordingly.
Moreover, accurate tracking records aid in resolving disputes between customers and suppliers (exclamation mark!). When a shipment goes missing or arrives late, clear records help identify the responsible party so that appropriate action can be taken. By keeping up-to-date documentation of every transaction, businesses protect themselves from costly legal battles and other conflicts related to delivery issues.
Overall, maintaining records of shipments is an integral part of any packing and shipping procedure. Not only does this ensure packages are delivered correctly but also helps resolve potential disputes quickly! Furthermore, it allows for more efficient data collection which leads to improved customer service performance over time - making record-keeping an invaluable task!
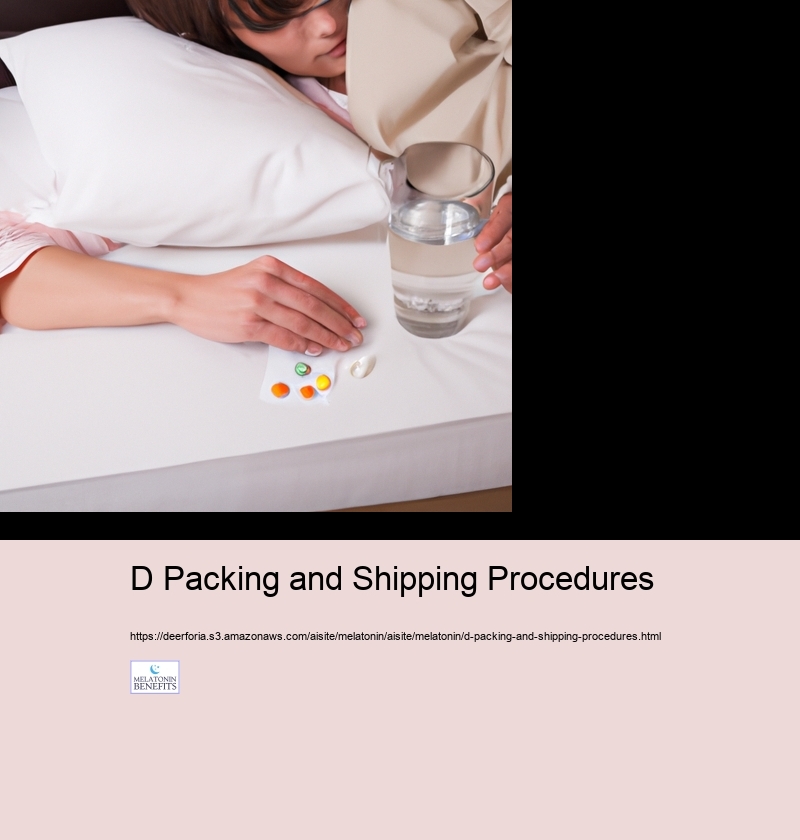